Isuzu KB P190. Manual — part 629
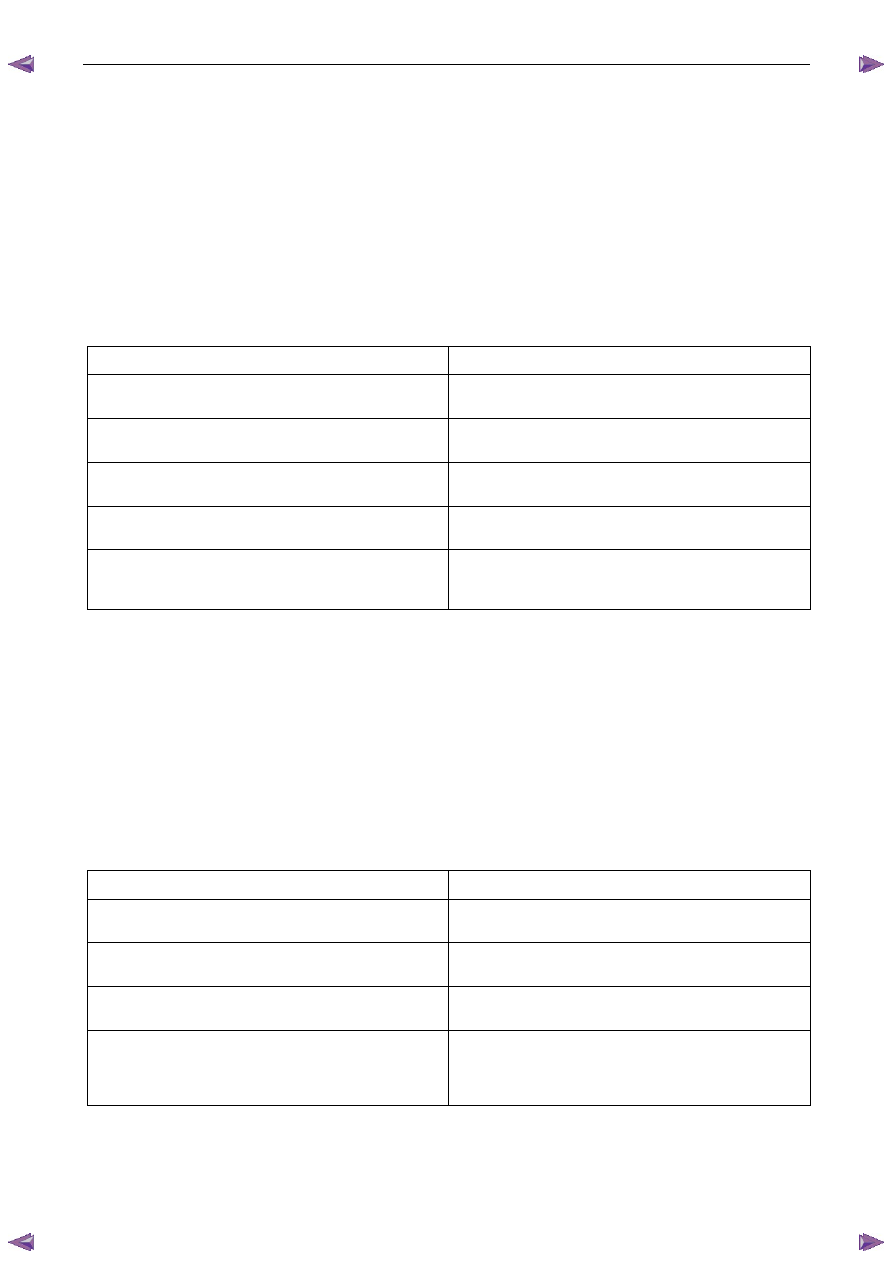
Engine Mechanical – V6
Page 6A1–37
2.13 Coolant in Combustion Chamber
Definition
Excessive white smoke and/or coolant type odour emitted from the exhaust pipe may indicate coolant in the combustion
chamber. Low coolant levels, an inoperative engine cooling fan or a faulty thermostat may lead to an over-temperature
condition which may cause internal engine component damage. A slower than normal cranking speed may indicate
coolant entering the combustion chamber.
1
Remove the spark plugs and inspect for spark plugs saturated by coolant and coolant in the cylinder bore.
2
Inspect by performing a cylinder leakage test, refer to 2.16
Cylinder Leakage Test. During this test,
excessive air bubbles in the coolant may indicate a faulty head gasket, cracked cylinder head or cracked cylinder
block.
3
Inspect by performing a cylinder compression test. Two cylinders side-by-side on the cylinder block, with low
compression, may indicate a failed cylinder head gasket, refer to 2.15
Engine Compression Test.
Cause Correction
Cracked intake manifold or faulty gasket.
Replace components as required, refer to 3.10
Intake Manifold Assembly – Complete.
Faulty cylinder head gasket.
Replace the cylinder head gasket, refer to 3.22
Cylinder Head Assembly.
Warped cylinder head.
Repair or replace the cylinder heads as required, refer to
3.22
Cylinder Head Assembly.
Cracked cylinder liner or block
Repair or replace the cylinder block and components as
required, refer to 4.7
Cylinder Block.
Cylinder head or cylinder block porosity.
Repair or replace the cylinder block or cylinder heads as
required, refer to 4.7
Cylinder Block or 3.22
Cylinder Head Assembly.
2.14 Coolant in Engine Oil
Definition
Foamy or discoloured oil or an engine oil overfill condition may indicate coolant entering the engine crankcase. Low
coolant levels, an inoperative engine cooling fan or a faulty thermostat may lead to an over-temperature condition which
may result in engine component damage. Contaminated engine oil and oil filters must be replaced.
1
Inspect the oil for excessive foaming or an overfill condition. Oil diluted by coolant may not correctly lubricate the
crankshaft bearings, resulting in component damage, refer to 2.10 Lower Engine Noise, Regardless of Engine
Speed.
2
Perform a cylinder leakage test, refer to 2.16
Cylinder Leakage Test. During this procedure, excessive air
bubbles in the engine coolant may indicate a faulty gasket or damaged component.
3
Perform a cylinder compression test. Two cylinders side-by-side on the cylinder block, with low compression, may
indicate a failed cylinder head gasket, refer to 2.15
Engine Compression Test.
Cause Correction
Faulty cylinder head gasket.
Replace the cylinder head gasket, refer to 3.22
Cylinder Head Assembly.
Warped cylinder head.
Repair or replace the cylinder heads as required, refer to
3.22
Cylinder Head Assembly.
Cracked cylinder liner or block
Repair or replace the cylinder block and components as
required, refer to 4.7
Cylinder Block.
Cylinder head, cylinder block or intake manifold porosity.
Repair or replace the cylinder block, cylinder heads or
intake manifold components as required, refer to 4.7
Cylinder Block, 3.22
Cylinder Head
Assembly or 3.10 Intake Manifold Assembly – Complete.
Engine Mechanical – V6
Page 6A1–38
2.15 Engine Compression Test
A compression pressure test of the engine cylinders determines the condition of the rings, the valves and the head
gasket.
Preliminary Steps
1
Ensure the battery is fully charged.
2
Remove the spark plugs from all cylinders, refer to 6C1-3 Engine Management – V6 – Service Operations.
N O T E
DTCs will set when the fuel system or the ignition
system is disabled and the engine is cranked.
Disregard DTCs that set under this condition.
3
Disable the fuel system by removing the fuel pump relay, refer to 8A Electrical Body & Chassis.
4
Start the engine to use any residual fuel from the fuel lines.
4
Disable the ignition coils by removing fuses 34 and 35, refer to 8A Electrical Body & Chassis .
5
Using Tech 2, command the throttle plate to wide open throttle.
Engine Cylinder Compression Test
1
Install the compression tester to cylinder number 1.
2
While observing the compression tester reading, turn the ignition to the START position for several seconds and
then allow the ignition to return to the ON position.
3
Record the highest compression reading obtained.
4
Repeat the engine compression test for each cylinder.
Test Result Evaluation
Normal engine compression pressure builds quickly and evenly to over 965 kPa. In addition, the lowest reading of an
engine cylinder should not be less than 70 percent of the highest reading. If any cylinder fails the compression test,
adding 15 ml of engine oil to the suspected cylinder may help isolate the following fault condition.
1
A fault condition in the piston rings will produce the following result:
•
A low compression on the first engine cycle
•
The compression tends to build-up with the succeeding engine rotation.
•
The compression improves with the addition of engine oil.
2
A fault condition in an intake or exhaust valve will produce the following result:
•
A low compression on the first engine cycle
•
The compression does not build with the succeeding engine rotation.
•
The compression does not improve with the addition of engine oil.
3
A fault condition in the cylinder head gasket will produce the following result:
•
A low compression on the first engine cycle
•
The compression does not build with the succeeding engine rotation.
•
The compression does not improve with the addition of engine oil.
•
The suspected cylinders are positioned adjacent to each other.
•
The engine oil may be contaminated with engine coolant.
•
The engine coolant may be contaminated with engine oil.
Once the fault has been identified, refer to the relevant service procedure and reinstall the removed components.
Using Tech 2, clear DTCs.

Engine Mechanical – V6
Page 6A1–39
2.16 Cylinder Leakage Test
A leakage test may be performed to measure cylinder/combustion chamber leakage. High cylinder leakage may indicate
one or more of the following:
•
worn or burnt valves,
•
broken valve springs,
•
stuck valve lifters,
•
incorrect valve lash/adjustment,
•
damaged piston,
•
worn piston rings,
•
worn or scored cylinder bore,
•
damaged cylinder head gasket,
•
cracked or damaged cylinder head, or
•
cracked or damaged engine block.
1
Disconnect the battery ground negative cable.
2
Remove the spark plugs from all cylinders, refer to 6C1-3 Engine Management – V6 – Service Operations.
3
Rotate the crankshaft to place the piston in the cylinder being tested at top dead centre (TDC) of the compression
stroke.
4
Install a commercially available cylinder head leak down tester into the spark plug hole.
N O T E
If required, hold the crankshaft balancer bolt to
prevent the engine from rotating.
5
Apply shop air pressure to the cylinder head leak down tester and adjust according to the manufacturers
instructions.
6
Record the cylinder leakage value. Cylinder leakage that exceeds 25 percent is considered excessive and may
require component service. In excessive leakage situations, inspect for the following conditions:
•
air leakage sounds at the throttle body or air inlet duct that may indicate a worn or burnt intake valve or a
broken valve spring,
•
air leakage sounds at the exhaust system tailpipe that may indicate a worn or burnt exhaust valve or a broken
valve spring,
•
air leakage sounds from the crankcase, oil level indicator tube, or oil fill tube that may indicate worn piston
rings, a damaged piston, a worn or scored cylinder bore, a damaged engine block or a damaged cylinder
head, or
•
air bubbles in the cooling system may indicate a damaged cylinder head or a damaged cylinder head gasket.
7
Perform the leakage test on the remaining cylinders and record the values.
2.17 Engine Oil Consumption Diagnosis
Definition
Excessive oil consumption (not due to leaks) is the use of 3 litres or more of engine oil within 10,000 kilometres. Prior to
performing oil pressure testing, a preliminary inspection of the vehicle should be performed. During the preliminary visual
inspection, the following likely causes of excessive oil usage should be investigated.
Cause Correction
External oil leaks.
Refer to 2.18
Engine Oil Leak Diagnosis.
Incorrect oil level or reading of the oil level indicator.
Check for the correct oil level, refer to 3.1
Engine Oil.
Incorrect oil viscosity.
Replace the engine oil, using the recommended SAE grade
of engine oil, refer to 3.1 Engine Oil.
Continuous high-speed driving or severe usage.
Service vehicle more frequently, refer to 0B Lubrication and
Service.
Crankcase ventilation system restricted or malfunctioning.
Repair or replace crankcase ventilation system components
as required, refer to 6C1-3 Engine Management – V6 –
Service Operations.

Engine Mechanical – V6
Page 6A1–40
Cause Correction
Worn valve guides and or valve stems.
Inspect and repair valves and valve guides as required,
refer to 3.22
Cylinder Head Assembly.
Worn or damaged valve stem oil seal.
Replace valve stem oil seals as required, refer to 3.22
Cylinder Head Assembly.
Piston rings broken, worn or not seated correctly.
Allowing adequate time for the piston rings to seat correctly,
replace piston rings as required, refer to 4.5 Pistons, Pins,
Rings, Connecting Rods and Big-end Bearings.
Piston rings incorrectly installed or not matched to cylinder
bore oversize.
Replace piston rings as required, refer to 4.5 Pistons, Pins,
Rings, Connecting Rods and Big-end Bearings.
2.18 Engine Oil Leak Diagnosis
Introduction
It is important to correctly identify the source of an engine oil leak. For example, a power steering fluid leak or spillage
during servicing can travel across the valley area of the engine and run-out the weep hole, which is located at the back of
the cylinder block. Failure to correctly identify the source of an engine oil leak can lead to unnecessary replacement of
engine components.
Most fluid leaks can be repaired by repairing or replacing the faulty component or resealing the gasket surface. However,
once a leak is identified it is important to determine and repair the cause as well as the leak itself.
Locating and Identifying the Leak
Inspect the leaking fluid and determine whether it is engine oil, transmission fluid, power steering fluid, brake fluid or
some other fluid. If unsure of the source of the leaking lubricant, a quick check of fluid levels should indicate where the
fluid is coming from, as one or more fluid level should be low.
Visual Inspection
Once the type of leaking fluid has been determined, a visual inspection of the affected system should be performed.
When performing the visual inspection:
1
Bring the vehicle to the normal operating temperature.
2
Park the vehicle over a large sheet of paper or other clean surface.
3
Leave the vehicle idling for 2-3 minutes, then check for dripping fluid.
4
If required, identify the type of fluid leaking and the approximate location of the leak.
5
Visually inspect the suspected area. A small mirror may assist viewing areas that are difficult to see normally.
6
Check for leaks at all sealing surfaces and fittings.
7
Check for any cracked or damaged components.
8
If the leak cannot be located, completely clean the entire engine and surrounding components, drive the vehicle at
normal operating temperature for several kilometres and then repeat Steps 3 to 8.
9
If the leak still cannot be located, proceed with either the Powder Method or Black Light and Dye Method as
outlined below.
Powder Method
1
Completely clean the entire engine and surrounding components.
2
Apply an aerosol type powder (e.g. foot powder) to the suspected area.
3
Operate the vehicle at normal operating temperature and at varying speeds for several kilometres.
4
Identify the source of the leak from the discoloration of the powder around the suspect components.
5
If required, use a small mirror to assist in viewing areas that are difficult to see normally.
6
Refer to Possible Causes for Engine Oil Leaks in this Section, and repair or replace components as required.
Black Light and Dye Method
A black light and die kit Tool No. J28428-E or a commercially available equivalent is available to technicians to aid in
engine oil leak diagnosis. When using a black light and die kit for the first time, it is recommended the technician read the
manufacturers instructions prior to using the kit.
1
Add the specified amount of dye, as per manufacturers instructions, into the engine or suspected source of the oil
leak.
2
Operate the vehicle at normal operating temperature and at varying speeds for several kilometres.
Нет комментариевНе стесняйтесь поделиться с нами вашим ценным мнением.
Текст